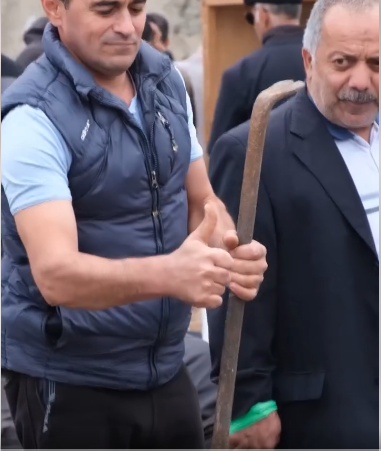
A Master Blacksmith at Work: Real Kusanaga Japanese Sword from Crowbar
The ancient art of Japanese sword-making, renowned for its precision, craftsmanship, and spiritual significance, has evolved over centuries. However, the work of modern artisans who carry forward this tradition, often blending old techniques with new materials, remains nothing short of awe-inspiring. One such example of a master blacksmith’s ingenuity is the transformation of an ordinary crowbar into a real Kusanaga Japanese sword—a striking demonstration of skill, creativity, and respect for the ancient swordsmithing craft.
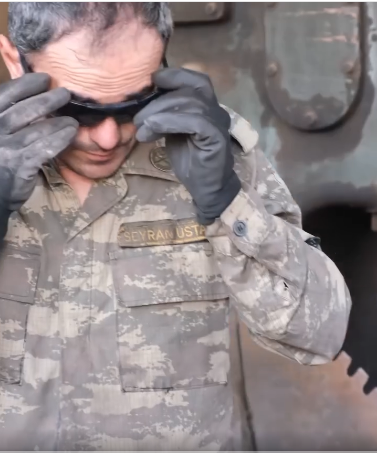
The Journey of a Kusanaga Sword
A Kusanaga sword is a traditional Japanese katana, known for its distinctive design, razor-sharp edge, and flawless balance. To make one, a blacksmith must employ a series of time-honored techniques passed down through generations. The blade is forged from high-carbon steel, folded multiple times to create the characteristic grain pattern known as “hada.” The result is a blade that is both hard and flexible, capable of holding an edge while remaining durable under stress.
In this case, the crowbar—a tool designed for leverage and pulling nails—undergoes an unexpected transformation into a high-performance katana. It may seem unusual at first glance, but the process highlights the versatility and creativity of the blacksmith. Crowbars are typically made from hardened steel, which is a good starting point for a sword blade. The blacksmith must first heat the crowbar to red-hot temperatures, making it malleable enough to be hammered into shape.
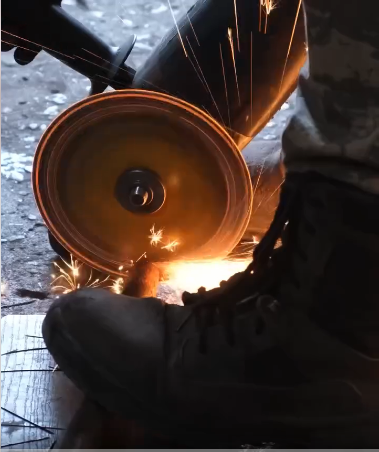
Forging the Blade
Once heated, the blacksmith begins the intricate process of drawing out the steel to form the blade. This includes several stages of hammering, folding, and welding to refine the structure. Each fold in the steel serves to remove impurities and evenly distribute carbon throughout the material, which is critical for achieving the desired balance between sharpness and strength. The crowbar’s steel, which was originally designed for strength and leverage, is now being reworked to provide the precision and sharpness that a katana demands.
During this phase, the blacksmith also begins shaping the tang (the portion of the sword that fits into the handle). The tang is essential for ensuring a secure and balanced grip, and it’s crafted with the same care and attention as the blade itself. As the process continues, the shape of the blade begins to take form—starting with a broader profile and gradually tapering toward a sharp edge, much like traditional katana blades.
The Heat Treatment and Edge
After shaping, the sword undergoes a heat treatment process known as “tempering.” This involves carefully heating the blade to a specific temperature and then quenching it in water or oil. This step hardens the steel, giving the sword its characteristic edge, but it also requires precise control to avoid warping or cracking.
To finish the blade, the smith refines the edge through polishing. This is one of the most time-consuming aspects of creating a katana. The blacksmith uses a series of progressively finer polishing stones to bring out the sharpness and reveal the intricate pattern of the steel. The final edge is razor-sharp, capable of slicing through materials with remarkable precision.
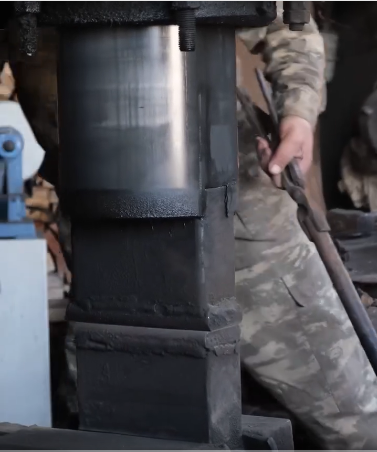
A Master’s Touch
The transformation of a crowbar into a Kusanaga sword requires not only technical expertise but also a deep respect for the tradition of Japanese sword-making. For the master blacksmith, each step of the process is an opportunity to demonstrate mastery over the materials and to channel the spirit of the samurai tradition. The result is a functional work of art—a blade that carries the weight of history while showcasing the innovative possibilities of modern blacksmithing.
Through the eyes of a true craftsman, an ordinary crowbar can become a symbol of transformation, illustrating how skill, dedication, and a passion for the craft can elevate the simplest tools into masterpieces.
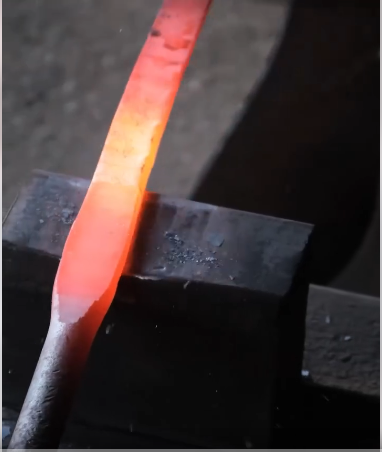